SHANG XIA
CASHMERE FELT
Created by expertly skilled master craftsmen, using similar techniques to those used when hand-felting fabric for Mongolian yurts, these sculpted garments are made in felt. Inspired by traditional Han dynasty clothing, this collection reflects the traditional elegance of Chinese style.
Each garment is unique and sculpted into a seamless shape to create a 3-dimensional garment in felt of Mongolian cashmere. Wrapped in style, one will surely remain warm in winter.
Felt was invented by herdersin the earliest antiquity. Working with traditional craftsmen, SHANG XIA has taken the felting process used for Mongolian yurts and adapted it to create warm coats and accessories in cashmere felt. Precious, high quality Mongolian cashmere is rubbed, teased and formed in a creative process more like sculpture than traditional tailoring. The Sculpture collection does not have a single seam or hem; is created without a single needle or thread; it is pure, dense cashmere.
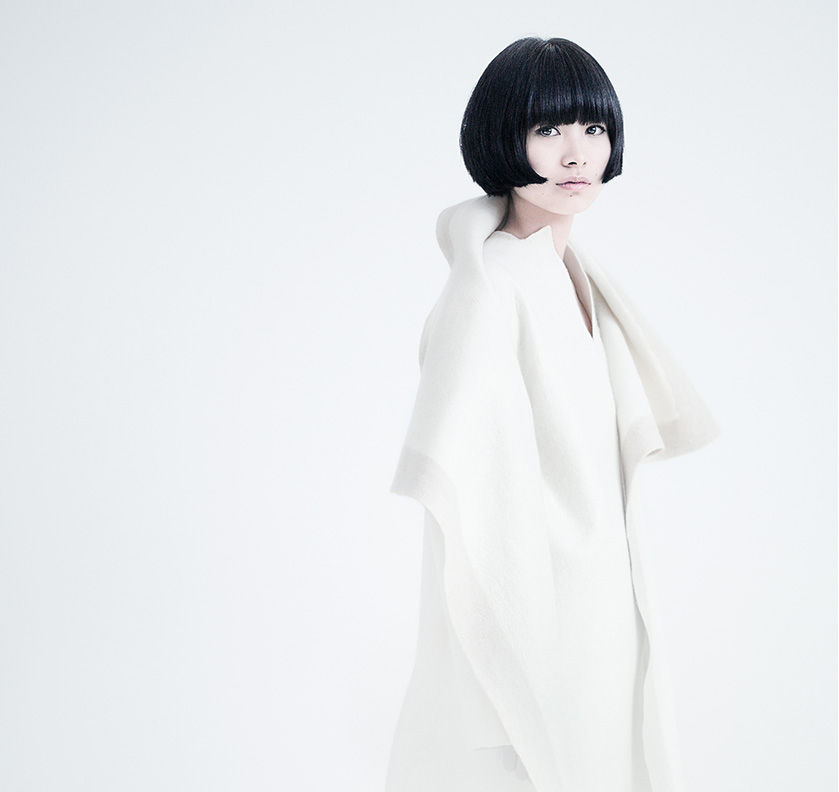


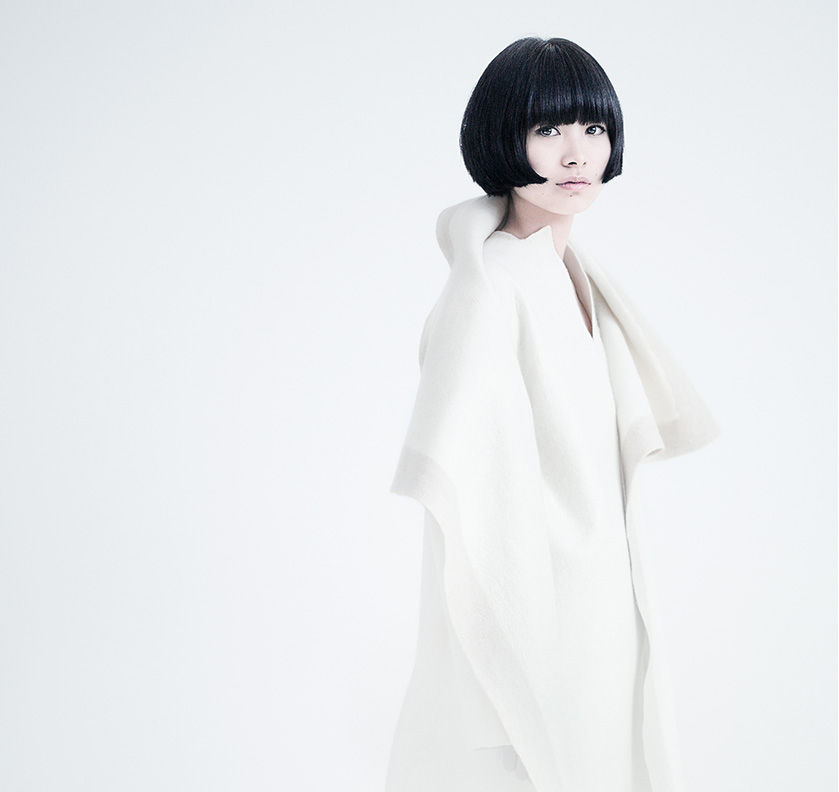
RELATED PRODUCTS

1.GATHERING
The goats are combed by hand with an iron comb, in spring when the weather starts to become warmer. The cashmere is extremely soft and very compact, it is a perfect material for felt making. Pieces of plants and goat waste must then be removed from the combed fleece, the fleece is then stored in this state.
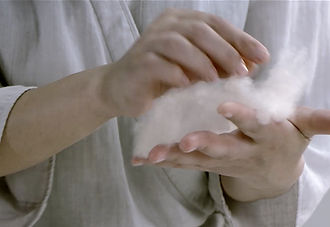
2. SELECTING THE CASHMERE
Selecting cashmere is one of the most important steps in felt making. The cashmere is selected according to different colors and qualities. The thinner and longer the fiber is, the better cashmere it is. SHANG XIA only chooses the finest cashmere for making its felt.

3. COMBING
Based on the desired size and thickness of the garment required, the appropriate amount of cashmere is put aside. Nomadic people first put the cashmere fibers on a rotating wheel hammered full of densely packed needles. As one hand turns the wheel, with the other hand one continues to add cashmere fiber so that eventually the combed cashmere becomes light and fluffy. Slowly all of the puffy fibers start to stick together and by this time almost all of the impurities have been cleaned away. It begins to look like a small-sized piece of light, fluffy felt. Generally the nomadic people first make small-sized felts and then based on their needs, piece the small felts together into a larger sized felt.
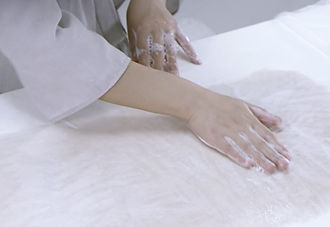
4. ROLLING THE FELT
These small sized cloud-like pieces of felt are spread out and pieced together to create one larger sized piece of felt. If one wants to make a thicker garment, an additional layer of small sized felt pieces is added. The first layer is horizontally laid out and the second layer is vertically laid out. Lightly pressed together, just boiled hot water is sprinkled onto the cashmere as in a desert after the rain, immediately after the water soaks into the cashmere, soap is pressed into the mass. A thick hand towel is used to soak up the water till dry and then this mass is placed over a wrung wet towel and rolled up into the towel. Dipping the hands in soap, the roll is rolled back and forth for 40 minutes or until the felt has stuck together. The towel is opened and the four corners are pulled apart. The rolling process is repeated for about 3 hours and during this second time boiled water is sprinkled on the rolled towel, washing out the impurities and creating a durable piece of felt. When unrolled, the remaining edges are trimmed and cut off with a ruler. This is the most detailed and studied part of the process and a knife cannot be used. Lastly, hooks are used to open up flat the fabric and untangle the tangled spots. The fabric is rinsed unhooked and hung up to dry. Thus a piece of felt is created.
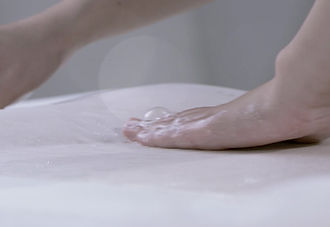
5. CREATING CLOTHING
The ready-made felt is laid on a table to dry. The clothing paper pattern is then laid on top of the fabric. The felt is sprinkled with boiling water, and dipping the hands in baby soap, pressed, rubbed and kneaded until it takes shape, constantly comparing the garment in process to the paper pattern. The garment slowly takes shape. It is then hung on a mannequin where further shaping and molding takes place so that the garment is fitted to every detail of the human form. Towels are then used to daub up the excess water. The garment is naturally air dried.

6. SHRINKING THE CLOTHING
At the final step, the garment is boiled in water to set the shape. As there is a certain amount of shrinkage in this process, the ultimate desired size of the garment depends on the skill, and experience of the felt worker in controlling the temperature and length of time the garment is boiled.
ZITAN WOOD
The collection embodies the concept of heaven and earth, where the original concept of rounded exterior lines and straight interior lines is now transformed to exterior lines that are straight and upright shielding one from the soft round curves of the interior lines.
The Da Tian Di collection is based on traditional Ming furniture construction principles, where each piece, is deftly hand crafted by a master craftsman.
The mortise and tenons of each element are skillfully fitted and hidden away allowing one to appreciate the pure beauty of the color, pattern and finish of the polished rare zitan wood surface.
Each piece of furniture is ergonomically designed. The wood is also treated to prevent warping and distortion.
The Chinese art of furniture making reached a peak during the Ming dynasty. The unique mortise and tenon construction means that very solid structures can be made without using a single iron nail. SHANG XIA has brought modern lines and design to traditional Chinese furniture by subverting the traditional round exterior/square interior device into a square exterior/round interior. In the process, it has pushed the boundaries of the carpenter's art. As well as respecting the Chinese tradition, SHANG XIA takes pride in perfecting every ergonomic detail, creating the most comfortable experience possible.
RELATED PRODUCTS
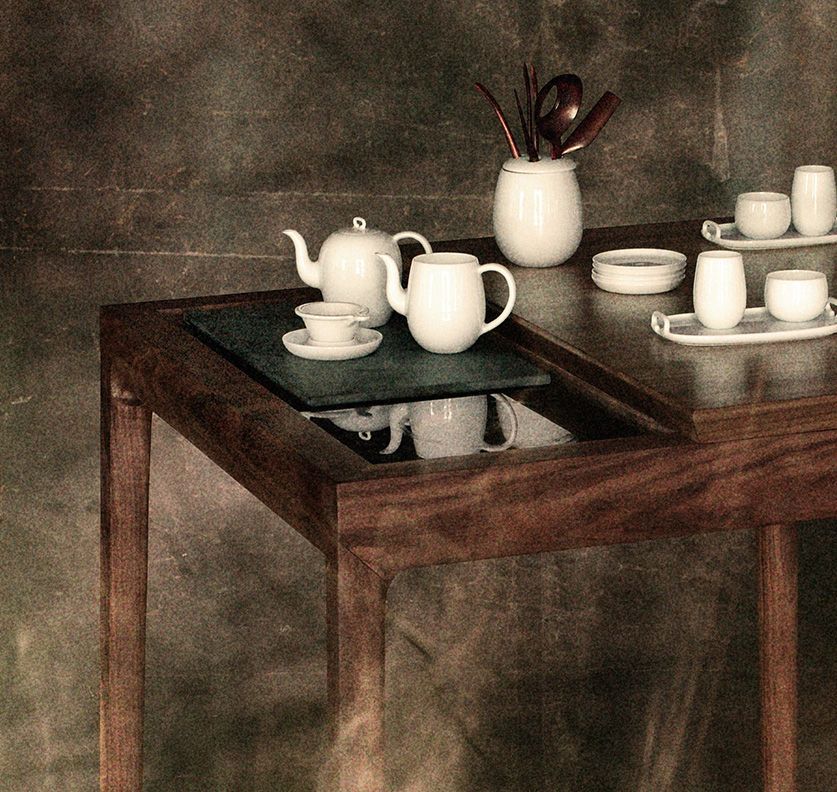
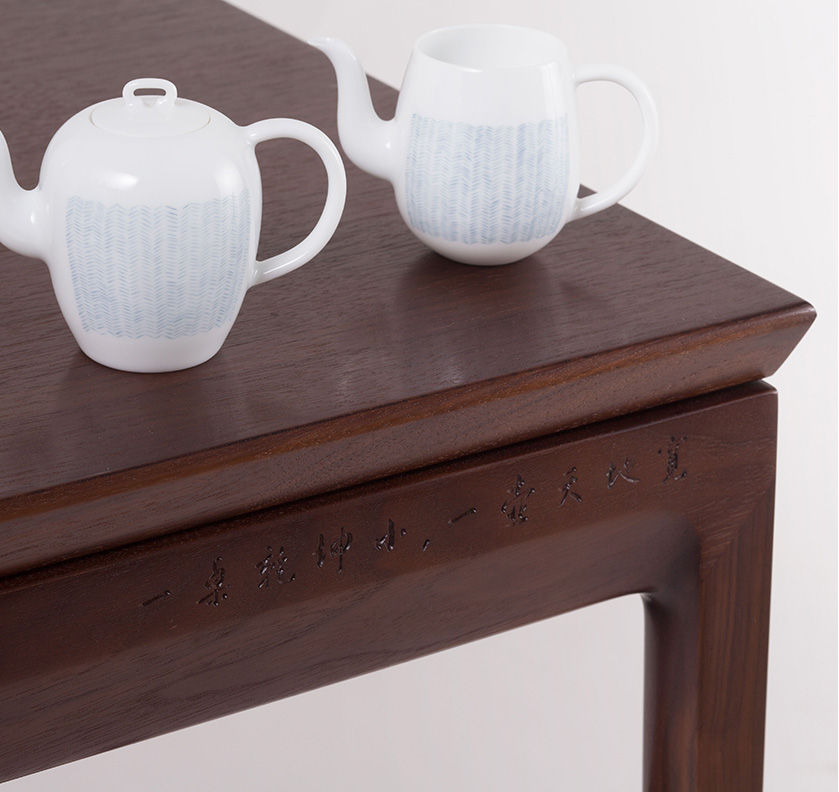

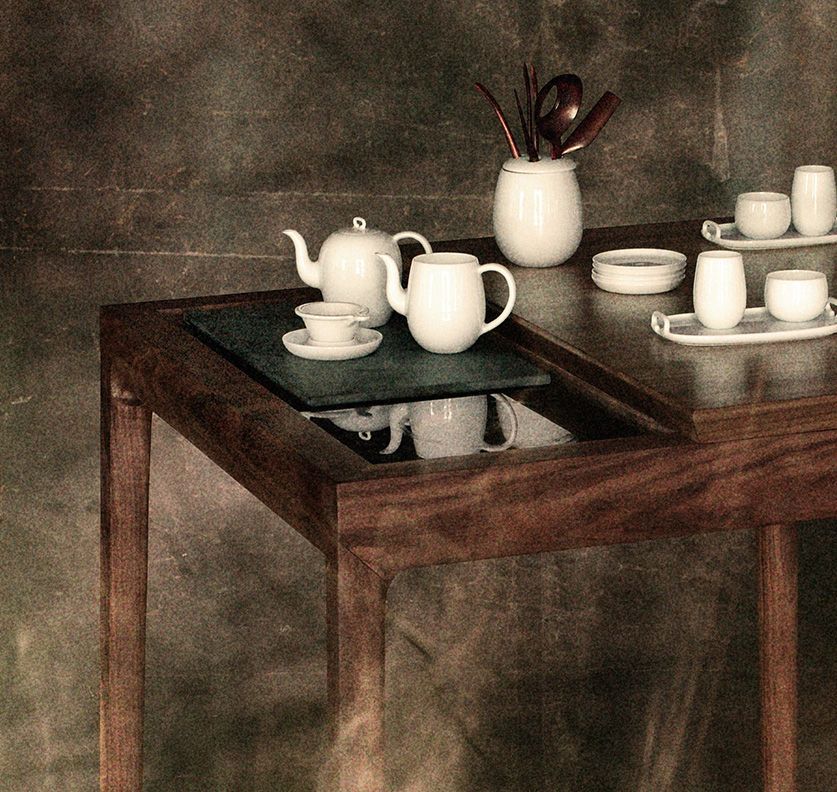

1. CHOICE OF TIMBER
Zitan is a very precious timber for two reasons. Firstly, the timber can only be used when it is several hundred years old, secondly, only 10% - 20% of the tree can be used to make furniture. Even to touch this rare wood is a matter of destiny! The carpenter prepared card models for each one of the furniture’s components, they were then cut from the timber according to the paper models. For example, a Ming style official hat chair has 42 components, including head rest, arm rest, back rest, apron, base pin and so on. It was said that in the Ming and Qing dynasties, all components for a piece of high quality hardwood furniture had to be from one single tree. Because of its rarity, the cutting craftsman shifu has to make the best, most efficient use of the timber.

2. DRYING
Though separated and cut, wood still has life. Water in the furniture will cause it to split, become loose or even rot. All of the timber needs to be treated in order to ensure that it is fully dry. The wood needs to be soaked in "wax water" for at least 6 months before all the moisture is removed from the wood. The stable wax is used to replace the active water elements. The wood will then remain permanently dry.
The biggest challenge to Chinese furniture carpenters has always been that solid wood expands and contracts with any slight change in temperature. Ancient carpenters invented the framing technique, a genius creation, however it did not tackle the problem completely. Master Gu spent more than 5 years inventing a technique exchanging water for wax within the wood, it is based on the heat exchange theory which ultimately prevents the wood from shrinking or distorting.

3. CONSTRUCTION
February 23, 2023
All Chinese furniture bases its construction on ancient architecture. The bridge, beam, post, pole and sparrow brace in architecture all have their equivalent within chair making, as the seat frame, edge, stretcher and brace are similar to elements in architecture.
Metal nails are never used when connecting components, instead, mortise and tenons are used to fit legs and waists together in waisted furniture, and also together with stretchers. Ancient people used the expression "will not fall in eternity" to describe the strength of mortise and tenons. Mortise and tenons can endure pressure from several directions making the furniture as stable and enduring as Mount Tai. In ancient times, due to the technical limit of carpentry, mortise and tenons were difficult to make and joints came loose easily. Today, with the help of precise mechanisms,
Master Gu has improved the accuracy of the joints by perfecting the quality of the mortise and tenons so that indeed they "will not fall in eternity".
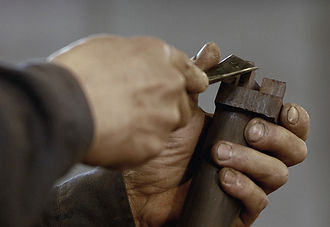
4. CARVING
GFThe carver placed various tools on the table. Zitan is famous for its hardness. If you hammer a nail into the timber, it will leave a mark and bend.Carving zitan requires several types of sharp knives. The carving master started from the top of the chair working his way down to the foot; from the skin of the timber he carved gradually inward, layer by layer much like a painter using knives as his brushes to create the image of the chair.

5. POLISHING
"It is not smooth enough. Keep on polishing, keep on. "Master Gu demanded of his staff. It is worth the effort to polish the furniture as if one is creating a needle from an iron post. In the zitan furniture craftsmen world the saying goes that zitan furniture is "10% shaping, 20% carving and 70% polishing ". Originally, the wood grain was not used for the purpose of decoration. But now, the beautiful grain pattern has become the most crucial and characteristic feature of the Ming style furniture. It established a new aesthetic value for Chinese furniture. Traditionally, waxed cough grass and thin cotton cloth were used to polish the wood. Master Gu used an extremely fine water-sand paper to polish and draw out the natural and hidden patterns in the wood grain, until the surface was as shiny as fine silk.
EGGSHELL PORCELAIN
Learning from Others, New Talent Arises.
Master Lu’s workshop is set in the countryside of Jingdezhen where he has purchased a small piece of land and like his ancestors who were part farmer and part craftsman, he too grows all kinds of vegetables, peppers, watermelons, corn, beans and potatoes on his land in front of the workshop.
In the Ming Dynasty, potters discovered how to make bowls less than one millimeter thick. Traditionally, eggshell porcelain was decorated with bright patterns, but SHANG XIA has developed a plain bowl. This porcelain is whiter, bigger, thinner, purer. In fact, because of the size of the bowls and the delicacy of the porcelain, only one piece in a hundred survives the firing process.


RELATED PRODUCTS

1. ONE CLAY, 72 PAIRS OF HANDS
"The Book of Jingdezhen Pottery" describes the pottery workshop in the 17th century, "Ceramics are made in kilns. Kilns belong to different families. Workers associate with their workshops. Workshops have masters. Division of work in ceramic production is fine."
Song Yingxing, a scientist in the Ming Dynasty, wrote in his book "Works of Science" that "one clay needs to pass through 72 pairs of hands before it is finally finished."
Today, in Master Lu’s eggshell porcelain workshop, the centuries long tradition is preserved. One worker takes charge of one process only.

2. MIXING INGREDIENTS
Porcelain stones and Kaolin clay mixed and crushed together in the muller. Though machinery has been introduced, the process is still the same as it always has been "at an even speed the muller stones grind together, so ingredients get well crushed and ground into a powder". Master Lu is the only one who knows the proportion of each ingredient, water and muller stones.

3. TURNING THE CLAY
The well mixed ingredients were kneaded into a paste, under the hands of the craftsman, the clay is worked into the shape of a bowl. Turning the clay mixture is the first step of molding. According to the craftsman, "turning is all about how you apply pressure. You have to be stable and even to keep air out of the clay mixture, a bubble destroys everything. You want your bowl to be round, you have to be hard and firm, otherwise it becomes out of shape." The technique and feel for the clay is not something one can learn in one or two years.
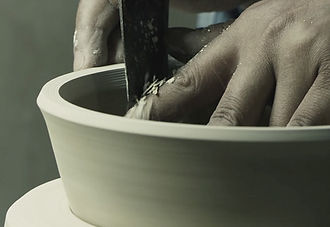
4. PARING AND TRIMMING
After turning, the thickness of the bowls wall was about 2-3 mm. Eggshell porcelain needs to be pared and fine trimmed using a knife at least one hundred times to achieve a fine 0.4 mm thickness as thin as eggshell and as thin as the cicada’s wing.
The paring craftsman, Lei, is a quiet man. Knife in hand, he focused on the bowl. Eggshell is extremely fragile and can easily be pierced if one tiny mistake is made. "I rely on my experience, sometimes on instinct too," said Lei. The inner and outer walls must be equally thin and smooth.
Fine trimming requires an even more precise execution. Each cut is a test for the executor. One has to have no distracting thought in mind, so that the beginning and end of every cut is identical, as sharp as the last. "Too hard a breath will cause a hand movement too big, destroying your work. Trimming men often say ‘success depends on every cut and every breath.’ It is quite true. They trim the wares, and they cultivate their minds, searching for peace and stability from within," Master Lu pointed out.

5. FIRING THE UNGLAZED BODY
The fine pared bodies were put on a wooden board and sent to the firing room. In a temperature of 750-800℃, they were fired for 1.5 hours.

6. ADDING WATER BEFORE GLAZING
The body wetting process needs serious care and attention. Craftsman Xiong, brushed water onto the bodies. Gaps or pinholes were filled and the bodies were cleaned and inspected for hidden air holes and dead mud.
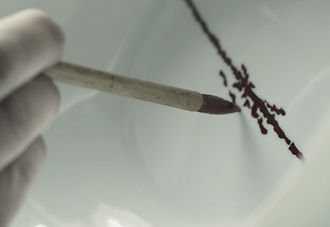
7. GLAZING
Glazing is the most crucial part in the whole process, and was performed by Master Lu himself. The varying viscosities of glazes create different final outcomes. The glaze has to be even on all parts of the body, the same thickness throughout. Seemingly easy, glazing is actually the most difficult part
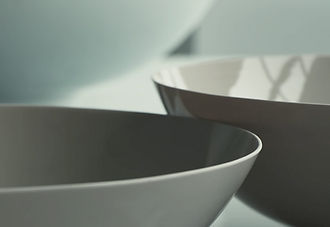
8. FINAL FIRING
The glazed bodies were placed into the kiln. At last, stone and clay are bound together by the skilled hands of the craftsman to create the most wonderful porcelain.
BAMBOO WEAVING
Around the path up the Cilao mountain, the wind blows through layers upon layers of bamboo like waves, the leaves rustling in the wind. As the poet Su Shi who studied on this mountain for 3 years, described “As one wears a thatch raincoat, in the rain and mist, one assumes a simple life”. So as before when Su Shi lived on the mountain, the people of the mountain today carry on the tradition of studying and living a simple way of life.
Bamboo weaving is an ancient craft. But where traditional craftsmen used only a basic weave and single strips, for the woven chinaware range SHANG XIA has developed a new technique, introducing double warp and double weft strips. This entirely new weaving space creates and entirely new effect: a subtle, textured sheet, woven with the thinnest bamboo strips ever cut, each less than half a millimeter thick.
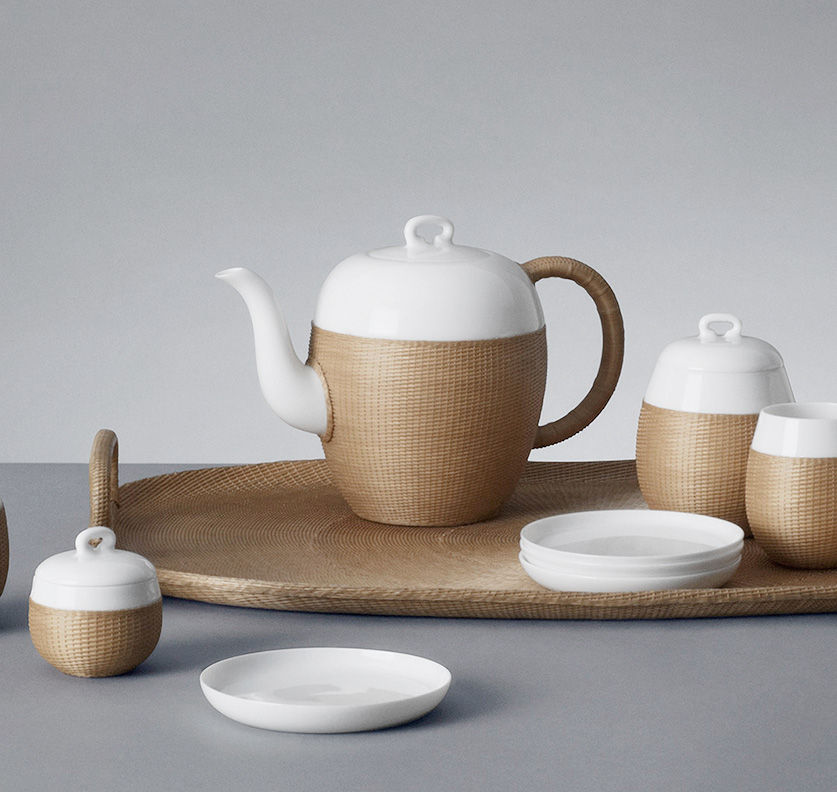

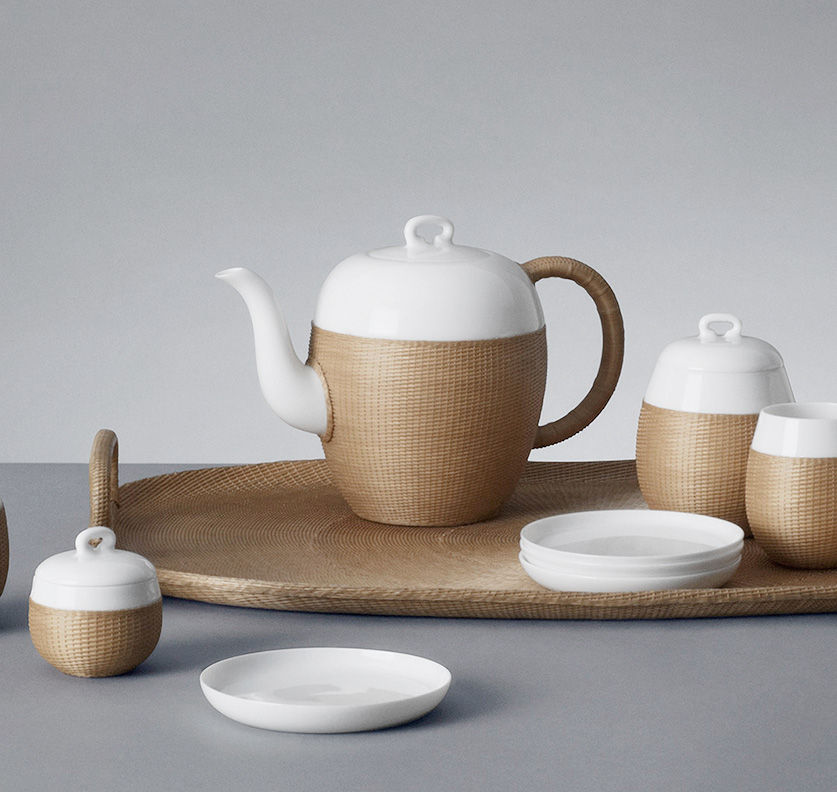
RELATED PRODUCTS

1. SILK-LIKE BAMBOO STRANDS
It was daybreak, the bamboo cutting Shifu (master) chopped his way to Cilao Mountain, a bamboo cutter hanging from his belt. The mountain and woods were shrouded in mist, his clothes soon became wet. The morning moisture was essential for the bamboo he was collecting, as when the sun came up the bamboo would turn hard and lose its flexibility.
Ci Bamboo (sinocalamus affinis) is a plant that requires shade, and favors moist areas. As the bamboo has beautiful lush branches and leaves, local people describe it as "reaching for the sky, collecting water and energy". According to the bamboo weaving Master Zhang who traveled with us, Ci bamboo grows in a water pit, in shade, away from the sun. Its shoots take only one year to grow into mature plants.

2. COLLECTING THE BAMBOO
Shifu was collecting one-year-old bamboo plants. He walked in water, and investigated. With merely one glimpse, he could tell which bamboo made the best material. He studied the direction of the bamboo hair in order to judge which plants were bitter bamboo, and which were sweet. Only the bitter plants are suitable for making bamboo woven ware. "Tall and straight, with long joints, that makes the best material" said Master Zhang. Some of the bamboo plants are crooked, their lives are determined by changes in direction. Only the strong and upright are true bamboo plants that can bravely face what is presented to them in life.
The cutters aimed carefully and cut the bamboo from the roots. Then they cut off the branches lengthways, and separated the bamboo into several segments using a hacksaw. Finally, they carried them down the mountain. This is usually a job for men.

3. SCRAPING THE CYAN (BAMBOO SKIN)
The women had to sharpen their knives and be well prepared to scrape the cyan, they had to be quick. The colloid layer has to be scraped from the stalk before the moisture has left the bamboo. A second later, cyan colored fine hair floated from the bamboo, leaving a faint trace of sweet fragrance.
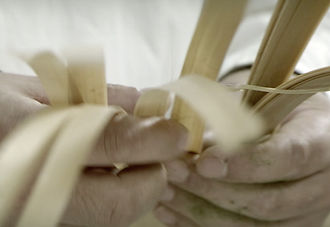
4. SEPARATING THE BAMBOO
The first step was to separate bamboo into blocks, as quickly and as accurately as possible, when the bamboo was still fresh and tender. The bamboo stalk is split into equally thick segments and these in turn are split into strips. Taking a smooth strip in the palm of the left hand, holding the strip with the thumb and the index finger one centimeter away from the end, the cutter uses her right hand, a third of the way down the slice the cutter cuts into the bamboo, slicing toward herself.
After hundreds of thousands of times of practice, a woman took two movements to complete the task. She cut a block, swung it up and down, then one bamboo slice fell off. She then cut again and swung, another slice off, and then another. All of the bamboo was sliced up in this way. Bamboo woven wares only require the first four layers of slices, sometimes only the first layer, since they have the best sheen.
Finally, the slices needed to be scraped again and again, until they were transparent, thinner than silk, less than 1mm.

5. DRYING THE SLICE
The delicately thin slices were hung and dried in a ventilated place. When a breeze drifted through, all of the bluish green pieces floated up and down in the wind, like waves rolling on the water. Looking at the fluttering green, the women can breath a relaxed breathe.,

6. SEPARATING STRANDS
The dried slices were ready for their last step. In general, a 1 cm wide bamboo slice can be separated into 2 to 48 strands (width ranging from 0.15 mm to 0.5 mm). With the strands separated, we could proceed to weaving.
Master Zhang spent over a decade studying bamboo woven wares. Well edified by natural landscapes and local cultures, he feels his bamboo cutting skills come from the traditions, environment and spirit of the land and its people.
Christie's Auction
‘ECHO’
A pair of red enameled eggshell porcelain bowls
Shang Xia 2015
Master Lu Jiande (Jingdezhen, China) for the porcelain and Ding Yi (Shanghai, China) for the painting
‘FUQI’ (HAPPINESS)
A set of four agate cups and stands
Shang Xia 2015
Master Yuan Xiaodi (Jiangsu, China)
‘RU YI’
A qinan incense brooch
Shang Xia
2015
Master Ren Gang (Shanghai, China)
Design The World’s Most Exclusive Shoes With Christian Louboutin’s Made

The craze of made-to-measure is catching up and Christian Louboutin is the latest designer to unveil the exclusive service. Loubi fans can now design the world’s most exclusive shoes with red soles with the launch of the French label’s Made to Measure facility.

The Made to Measure process is unique and utterly luxurious as one-of-a-kind shoes and boots are meticulously created from personal measurements, and crafted with care by a number of expert hands. Rolling out infinite possibilities, “It is an opportunity for the people who love my shoes to step into our world and create something truly one-of-a-kind” asserts Monsieur Louboutin.

Christian Louboutin makes it possible to fulfill a client’s dream for a perfect shoe!

The craze of made-to-measure is catching up and Christian Louboutin is the latest designer to unveil the exclusive service. Loubi fans can now design the world’s most exclusive shoes with red soles with the launch of the French label’s Made to Measure facility.

The embodiment of Ralph Lauren's passion for impeccable quality and exquisite design, Ralph Lauren timepieces feature the finest in Swiss Made mechanical movements and the world's most luxurious materials. Unique and immediately recognizable, they are the ultimate expression of the Ralph Lauren lifestyle.

The embodiment of Ralph Lauren's passion for impeccable quality and exquisite design, Ralph Lauren timepieces feature the finest in Swiss Made mechanical movements and the world's most luxurious materials. Unique and immediately recognizable, they are the ultimate expression of the Ralph Lauren lifestyle.

The embodiment of Ralph Lauren's passion for impeccable quality and exquisite design, Ralph Lauren timepieces feature the finest in Swiss Made mechanical movements and the world's most luxurious materials. Unique and immediately recognizable, they are the ultimate expression of the Ralph Lauren lifestyle.

The embodiment of Ralph Lauren's passion for impeccable quality and exquisite design, Ralph Lauren timepieces feature the finest in Swiss Made mechanical movements and the world's most luxurious materials. Unique and immediately recognizable, they are the ultimate expression of the Ralph Lauren lifestyle.